In the world of manufacturing and woodworking, the laminate press machine stands as a crucial tool, enabling the creation of high-quality laminated surfaces. Whether used in the production of furniture, flooring, or decorative panels, this machine plays a vital role in ensuring durability and aesthetics. This blog will delve into the workings, types, applications, and benefits of laminate press machines, providing a clear understanding for industry professionals and enthusiasts alike.
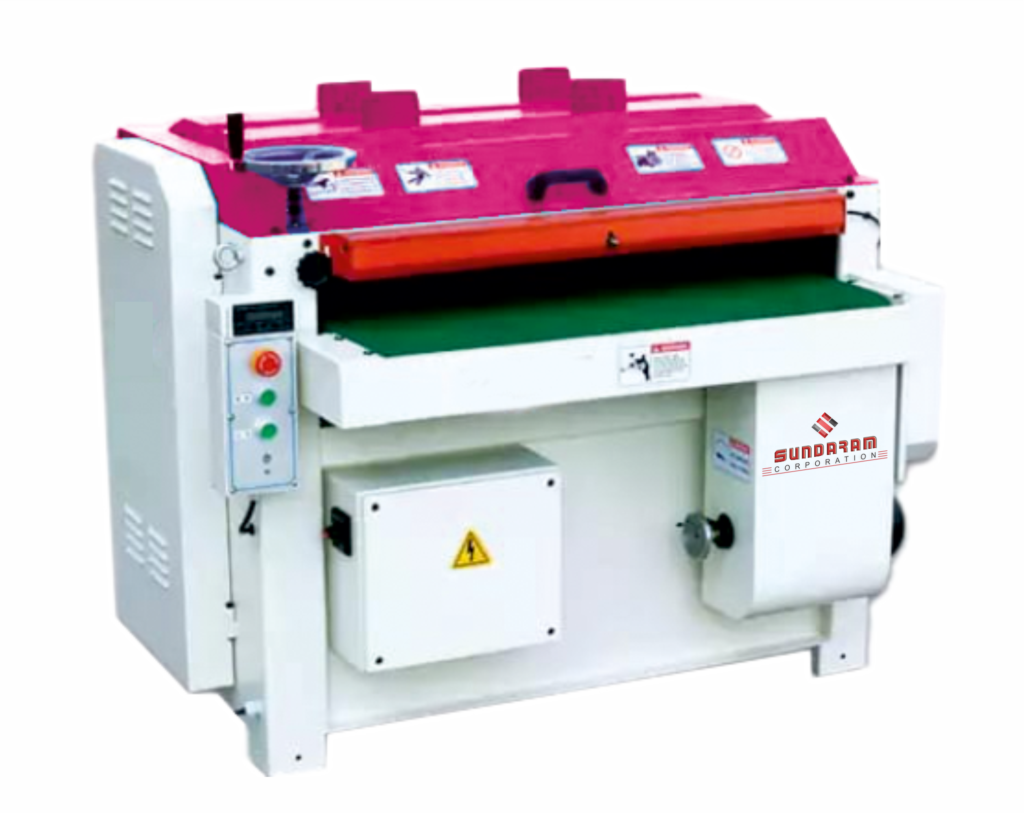
What is a Laminate Press Machine?
A laminate press machine is a specialized piece of equipment used to bond layers of material together to form a laminate. The process typically involves applying heat and pressure to a core material, such as wood or MDF (Medium Density Fiberboard), and bonding it with a decorative surface layer, like veneer, melamine, or paper. The result is a strong, durable, and aesthetically pleasing surface that is commonly used in furniture, cabinetry, flooring, and wall panels.
Types of Laminate Press Machines
Laminate press machines come in various types, each designed for specific applications and production requirements. Here are the most common types:
- Hot Press Machines: These are the most widely used laminate press machines in the industry. They use heated platens to apply uniform pressure and heat, ensuring a strong bond between the layers. Hot press machines are ideal for large-scale production and can handle a wide range of materials.
- Cold Press Machines: Unlike hot press machines, cold press machines do not use heat. Instead, they rely solely on pressure to bond the layers. Cold press machines are typically used for applications where heat-sensitive materials are involved or when a quick turnaround is required.
- Continuous Press Machines: These machines are designed for high-volume production and operate continuously, feeding materials through the press at a constant rate. Continuous press machines are highly efficient and are commonly used in large-scale manufacturing plants.
- Membrane Press Machines: These machines use a flexible membrane that conforms to the shape of the workpiece, allowing for the lamination of complex and curved surfaces. Membrane press machines are often used in the production of high-end furniture and cabinetry.
Applications of Laminate Press Machines
Laminate press machines are used in a variety of industries, each with unique requirements and applications. Some of the most common applications include:
- Furniture Manufacturing: Laminate press machines are widely used in the production of furniture, where they are used to create durable and visually appealing surfaces for tables, chairs, cabinets, and more.
- Flooring: In the flooring industry, laminate press machines are used to produce laminated flooring, which is known for its durability, resistance to wear, and aesthetic appeal.
- Decorative Panels: These machines are also used to create decorative wall panels, which are often used in interior design to add a touch of elegance and sophistication to spaces.
- Countertops: Laminate press machines are instrumental in the production of laminated countertops, which are popular in kitchens and bathrooms for their durability and ease of maintenance.
Benefits of Using a Laminate Press Machine
The use of a laminate press machine offers several key benefits:
- Enhanced Durability: The lamination process enhances the strength and durability of the core material, making it resistant to wear, moisture, and other environmental factors.
- Cost-Effective: Laminated products are often more cost-effective than solid wood or stone alternatives, making them a popular choice in both residential and commercial settings.
- Aesthetic Appeal: Lamination allows for a wide range of design options, from wood grain patterns to vibrant colors, enabling manufacturers to create products that meet the aesthetic preferences of consumers.
- Efficiency: Modern laminate press machines are highly efficient, allowing manufacturers to produce large quantities of laminated products in a relatively short amount of time.
- Customization: With the right machine, manufacturers can easily customize the thickness, design, and finish of laminated products to meet specific customer requirements.
No comment